Extrusionsblasformen: Extrusion als erster Verfahrensschritt
Als erster Verfahrensschritt beim Extrusionsblasformen (auch Extrusionsblasen genannt) wird in Pulver- oder Granulatform vorliegender thermoplastischer Kunststoff einem Extruder zugeführt. Die im Extruder befindliche Schnecke zieht mit ihrer Drehbewegung das Material im Bereich der Einzugszone ein, verdichtet das Material, wobei die das Granulat umgebende Luft über den Materialtrichter entweicht. Dieser Vorgang wird auch als "Entgasung" bezeichnet.
Die Kunststoffmasse wird weiter in Förderrichtung transportiert und erhält über die beheizte Wandung des Schneckenzylinders und über die aus der Drehbewegung entstehende Reibungswärme die zum aufschmelzen erforderliche Temperatur.
Die im Laufe der kontinuierlichen Fertigung durch die Schneckendrehung auftretende Reibungswärme kann des öfteren den Wärmebedarf zum Aufschmelzen des Granulates übersteigen. Aus diesem Grund sind die Extruder oftmals mit einer Gebläsekühlung ausgestattet, die die überschüssige Wärme abführt.
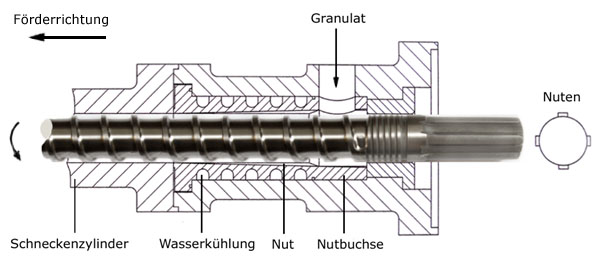
Um die Förderleistung zu erhöhen und die für das Extrusionsblasformen sehr wichtige Förderkonstanz zu verbessern wird bei der Verarbeitung von Polyolefinen die Einzugszone des Extruders mit einer Nutbuchse ausgerüstet. Die Nuten, die auf einer Länge von meist 3 x Schneckendurchmesser konisch auslaufen, sollen verhindern daß Granulatkörner auf der Schnecke anhaften und sich dann nur noch mit der Schnecke stationär drehen, statt von der Schneckenflanke weitergefördert zu werden. Neu entwickelte Einzugszonenkonzepte setzen auch mit wendelförmigen Nuten versehene Nutbuchsen in größeren Längenverhältnissen ein.
Die Einzugszone wird in der Regel mit Wasser gekühlt. Um die thermischen Verluste an der Verbindundsstelle zwischen Nutbuchse und beheiztem Schneckenzylinder so klein wie möglich zu halten, werden die Kontaktflächen zwischen Einzugszone und Schneckenzylinder auf eine schmal gehaltene Kreisringfläche reduziert.
Bei harten Materialien wie z.B. Polycarbonat (PC) werden keine Nutbuchsen eingesetzt, da sonst die Schneckenbelastung und damit einhergehend die Stomaufnahme des Extrudermotors zu stark ansteigt.
Die Förderleistung eines Extruders ist von folgenden Gegebenheiten abhängig:
• Dem Schneckendurchmesser
• Der Schneckensteigung
• Der Gangtiefe der Schnecke
• Der Schneckendrehzahl
• Der Gestaltung der Einzugszone
• Der Temperatur der Einzugszone
• Dem Schüttgewicht des zugeführten Granulates
• Der Temperatur des Schneckenzylinders
• Der Viskosität der Kunststoffschmelze
• Dem Strömungswiderstand des Schlauchkopfes
Extruderdrehzahlkorrektur
Da beim Extrusionsblasformen in einer vorbestimmten Zeitdauer immer genau die gleiche Menge plastifiziertes Material bereitgestellt werden soll, aber Einflussfaktoren wie Schüttgewicht, Chargenschwankungen und sich verändernde Temperaturen im Bereich Extruder und Schlauchkopf (und den daraus resultierenden Veränderungen in der Viskosität des Extrudates) die Förderleistung immer wieder verändern, setzt man eine Extruderdrehzahlkorrektur ein.
Dieses setzt man Maschinentechnisch um, indem man die Zeitspanne zwischen dem Signal "Blasform in oberer Endlage" und dem mit einer Fotozelle abgefragten Signal "richtige Länge des Vorformlings erreicht" miteinander vergleicht. Wenn die Zeitspanne zu gering oder Null ist, wird die Extruderdrehzahl automatisch reduziert, wenn die Zeitspanne zu groß ist wird die Drehzahl erhöht. Die Vorgabezeiten / Sollwerte dieser Formwartezeit liegen meist im Bereich von 0,1 bis 0,4 Sekunden. Bei sehr langen Artikeln kann sich diese Regelung aber auch sehr "aufschaukeln" sodaß eine konstante Fertigung nicht mehr möglich ist. In diesem Falle muß die Drehzahlkorrektur ausgeschaltet werden, man muss längere Formwartezeiten in Kauf nehmen.
Extrusionsblasformen: Formen des Vorformlings mit dem Schlauchkopf
Am Beispiel eines Pinolenkopfes.
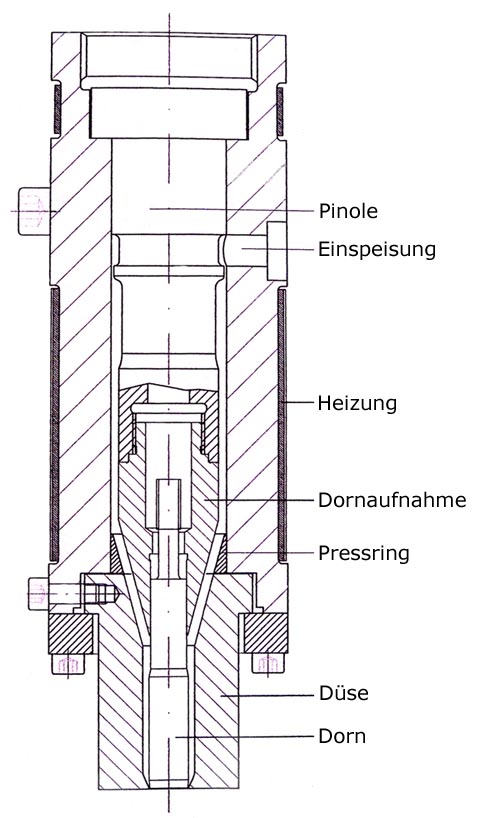
Beim Extrusionsblasformen wird die Kunststoffschmelze vom Extruder über die Einspeisungsbohrung in den Schlauchkopf gefördert, trifft dort auf die Ringnut der Pinole und umströmt diese. Auf der rückwärtigen Seite der Ringnut trifft der durch die Pinole getrennte Materialstrang wieder zusammen und verschweißt hier. Die Kunststoffschmelze strömt anschliessend über den Steg der Ringnut nach unten. Im weiteren Verlauf des kreisringförmigen Kanales findet ein Druckausgleich und damit eine Angleichung der Strömungsgeschwindigkeit statt.
Der Pressring der vom Massedruck gegen die Düse gepresst wird dichtet die Verbindung zu der radial verstellbaren Düse ab. Durch die angeflanschten Kopfwerkzeuge ( Dorn und Düse) wird der Durchmesser und die Wanddicke des extrudierten Vorformlings an die Anforderungen des zu produzierenden Blasformteiles angepasst. Der Dorn wird mittels einer Zugstange und Servohydraulik- Stellzylinder (hier nicht abgebildet) während jedes Produktionszykluses in axialer Richtung verschoben. Aufgrung der konischen Gestaltung des Dornes ändert sich dadurch die Wandungsdicke des Vorformlings und in der Folge die Wanddicke des produzierten Blasformteiles.
Dieser Kopftyp ist nur für das Extrusionsblasformen mit kontinuierlicher Extrusion einsetzbar.
Dieser Schlauchkopf- Typ hat folgende Vorteile:
Relativ preiswert in der Herstellung
Die Bauform ermöglicht kleine Mittenabstände
Die Wanddickenregulierung ist mechanisch nicht so aufwändig.
Dieser Schlauchkopf- Typ hat folgende Nachteile:
Schlechte Materialwechselzeiten da sich an der Schweißstelle der Ringnut Ablagerungen / Farbpigmente sammeln die nur sehr langsam weggespült werden. Es bildet sich durch ungleichmäßige Temperatur- Rundumverteilung die aus differierenden Schmelzetemperaturen herrührt ein ungleichmäßiges Strömungsverhalten. Diesem Strömungsverhalten muß durch zentrieren bzw. dezentrieren der Düse entgegengewirkt werden. Da sich die Temperaturverhältnisse während der Fertigung und ganz besonders in der Anlaufphase verändern, muss die Düsenposition des öfteren nachjustiert werden, weil sich sonst eine ungleichmässige Rundumverteilung der Wanddicke im Blasformteil ergibt.An der Stelle an der der Materialstrang wieder auf der Pinole verschweißt wurde können sich im Blasformteil Laufstreifen und Dünnstellen bilden.
Schlauchkopf für Mehrfach- Fertigung.
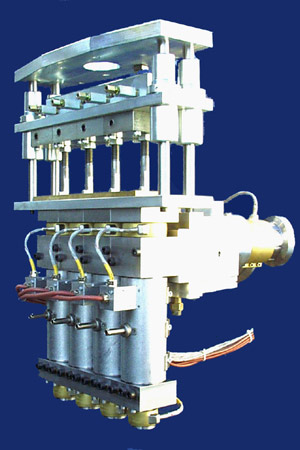
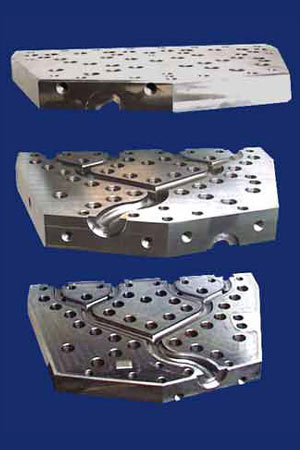
Mit diesem Schlauchkopf werden gleichzeitig vier nebeneinander austretende Vorformlinge hergestellt, um in einem einzigen Maschinenzyklus vier Artikel fertigen zu können. Dieser Schlauchkopf wird zusätzlich mit zwei unterschiedlich eingefärbten Materialien aus zwei Extrudern beschickt. Damit werden Artikel produziert, die aus zwei verschiedenen Schichten bestehen. Die in der rechten Abbildung sichtbaren (demontiert gezeigten) Verteilerplatten führen die aus zwei Extrudern geförderten Kunststoffschmelzen gleichmäßig aufgeteilt an die vier einzelnen Schlauchköpfe heran.
Weiterführende Seiten:
Blasformen mit kontinuierlicher Extrusion
Blasformen mittels Speicherkopf und diskontinuierlicher Bereitstellung des Vorformlings