Blowmolding with accumulator head/discontinuous preform feed.
When producing blowmolded articles for technical use(e. g., air ducts, fuel tanks, drums, canoes, rainwater tanks, oil tanks) the preform is fed discontinuously instead of being continuously extruded.
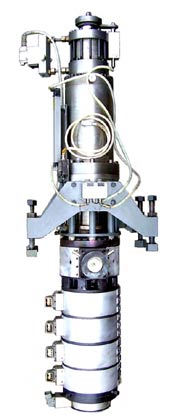
Blowmolding technology: FIFO Accumulator head with ring piston accumulator
From the technical point of view, in this process an accumulator head is used which accumulates the plastic melt, which is then continuously fed by the extruder. The head stores it temporarily and presses it within short intervals (1 x 2 seconds) out of the die head by means of a hydraulically operated circular ring piston. In most cases, the extruder is in uninterrupted operation.
Today, an accumulator head normally is designed on the basis of the FIFO principle (first in – first out). This means that the melt which is fed by the extruder into the accumulator head first, also is ejected first. This process allows uniform retention times and a high temperature constancy of the plastic melt.
Figure: Kautex 5L FIFO accumulator head
This blowmolding process is applied due to the following reasons:
Blowmolding technology – Requirements based on the extrudate:
The plastic melt has low stability. For this reason, the parison/preform coming out of the die gets longer due to its own weight.
This lengthening effect becomes greater
• the longer the parison has to be
• the lower the viscosity of the plastic melt is ((e. g., when processing ABS or
polycarbonate)
• the thicker the article walls need to be.
(Here, the time to cool down the blowmoulded article und the longer period of time the parison would need to continue to stick to the die during continuous extrusion.)
These reasons are decisive for the selection of the production process fitting to the article requirements:
Blowmoulding technology – Requirements based on mechanical engineering i. e. machine construction:
The blowmolding tools for the articles produced in this blowmolding technology normally are considerably greater and heavier, the necessary clamping forces are also considerably higher. Therefore, the clamping units of the blowmolding machines used also are greater and essentially heavier. For this reason, a movement of the clamping unit including blowmould tool underneath the parison (to give space to the preform continuously being produced in case of continuous extrusion), requires technically complex designs. In most cases this even would bring no advantage due to the problem of the lengthening of the preform.
Blowmold cycle when using accumulator head:
Blowmolding cycle in productions with accumulator head
In comparison to productions via continuous extrusion, downtimes here are essentially higher (in case of continuous extrusion mostly between 1,5 to 3 seconds; in case of the diagramme above showing a cycle of a Kautex KB 50 with accumulator head and removal gripper, for instance, 21 seconds). Due to the fact that the cycle time depending on the wall thickness of the article to be produced, this process only becomes profitable with higher wall thicknesses.
(In the current example the wall thickness is approximated 3 mm). In the cycle shown below downtimes sum up to 38 %.)
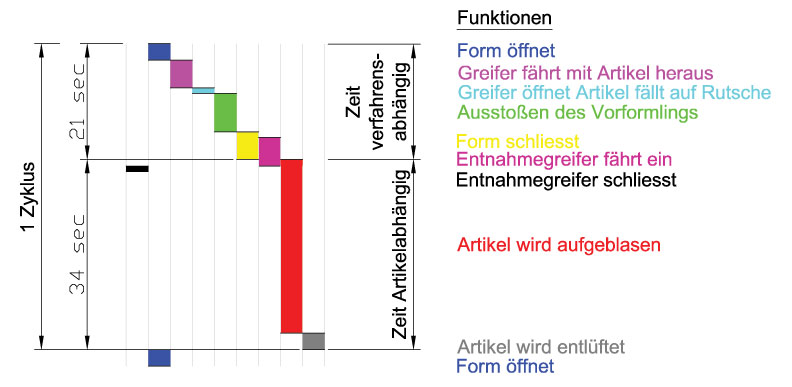
When producing an article with a wall thickness of 1 mm, the inflation time would take approximately 20 seconds less. In this case, the process-related periods of time would have an impact of 60 % in the entire production cycle. For this reason, it is advisable not to produce blowmolded articles with thin wall thicknesses unless these articles are to be produced for which the lengthening of the preform is a decisive quality criteria.
Example: Blowmolding Machine Kautex KB 25 with 5 ltr. accumulator head for the production process described before.
Further pages:
Extrusion blowmolding: Extrusion as the first process step
Blow molding plastic containers by continuous extrusion